Beschichtungsaufbau der Serienlackierung
In der Regel besteht eine Autoserienlackierung heute aus vier Schichten (ca. 0.100 Millimeter), die in mehreren Arbeitsgängen mit unterschiedlichen Verfahren appliziert werden. Jede Schicht hat bestimmte Aufgaben zu erfüllen. Dazu müssen die einzelen Schichten genau aufeinander abgestimmt sein.
Der Beschichtungsaufbau kann in 4 Gruppen eingeteilt werden:
Haftbeschichtung
Nachdem die Rohkarrosserie von Ziehfett, Rostschutzölen, Schleifstaub und Spähnen in alkalischen Reinigungs- und Entfettungsbädern gesäubert wurde, wird nach einem Spühlgang die Phosphatschicht im Sprüh- oder Tauchverfahren aufgetragen. Diese Schicht ist die Erste, die auf das zu lackierende Blech appliziert wird. Durch diese schichtbildende Zinkphosphatierung (ca. 0.003 mm) wird an der Substratoberfläche (Materialoberfläche) eine optimale Konversionsschicht gebildet. Unter Konversionsschichten versteht man nichtmetallische, meist anorganische, sehr dünne Schichten auf einer Metalloberfläche, die in der Regel durch chemische Reaktion einer wässrigen Behandlungslösung mit dem metallischen Untergrund erzeugt werden. Diese Vorbehandlung steigert die Lackhaftung und den Korrosionsschutz bei der kathodischen Tauchlackierung (KTL).
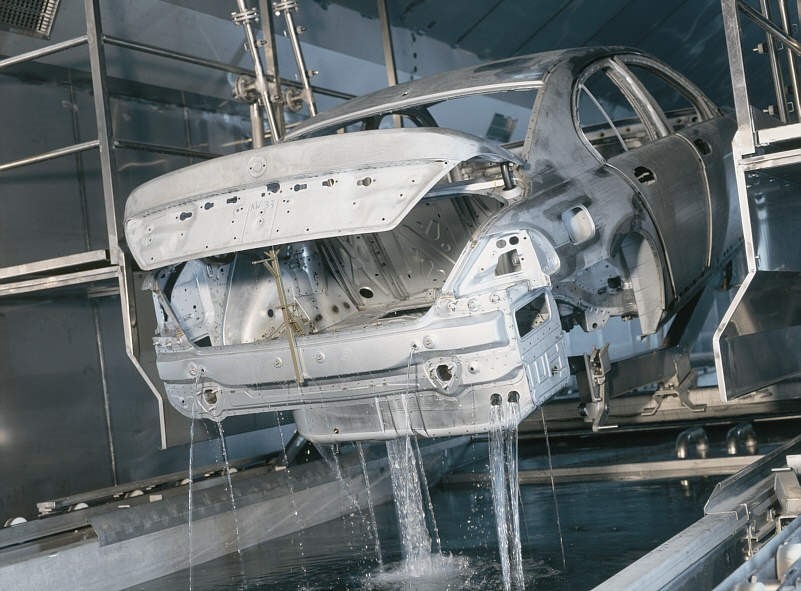
Grundbeschichtung
Die Grundierung ist die zweite Schicht bei einer Lackierung und wird auf der Phosphatschicht aufgetragen. Sie sorgt für noch eine bessere Haftung für die nachfolgenden Schichten. Die Grundierung (ca. 0.020 Millimeter)wird meist durch das Tauchbad aufgetragen, wobei sie in alle Hohlräume und Ecken der Karosserie eindringt. Diese kathodische Tauchlackierung, kurz KTL, ist die Basis für einen umfassenden Korrosionsschutz. Dabei wird die kathodische Karosserie (negativ geladene Karosserie) durch einen wässrigen, leitfähigen Tauchlack gefahren, in dem die positiv geladenen Lackteilchen sich an die Karosserie anheften und eine geschlossene und gleichmäßige Beschichtung bilden.
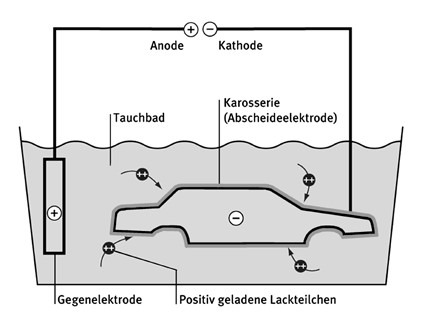
Zwischenbeschichtung
Dann folgt der Auftrag des so genannten Füllers (ca. 0.030 Millimeter), der gleich mehrere Aufgaben zu erfüllen hat. Neben dem Schutz vor Steinschlag gleicht er kleinere Unebenheiten und Schleiffrillen auf der Oberfläche aus, füllt sie sozusagen auf. Zudem sorgt er dafür, dass der anschließende Decklack besser haften kann. Der Füller ist im Falle von Kratzern unter der farbgebenden Lackierung meist als grauweisse Schicht zu erkennen. Ist diese Schicht nicht verletzt, kann man davon ausgehen, dass der Korrosionsschutz noch intakt ist. Es gibt heute jedoch auch Füller, die bereits Farbpigmente enthalten und so die Deckkraft und Brillanz des nachfolgenden Basislacks verstärken. Der Füller wird meist durch das elektrostatische Spritzverfahren aufgetragen.
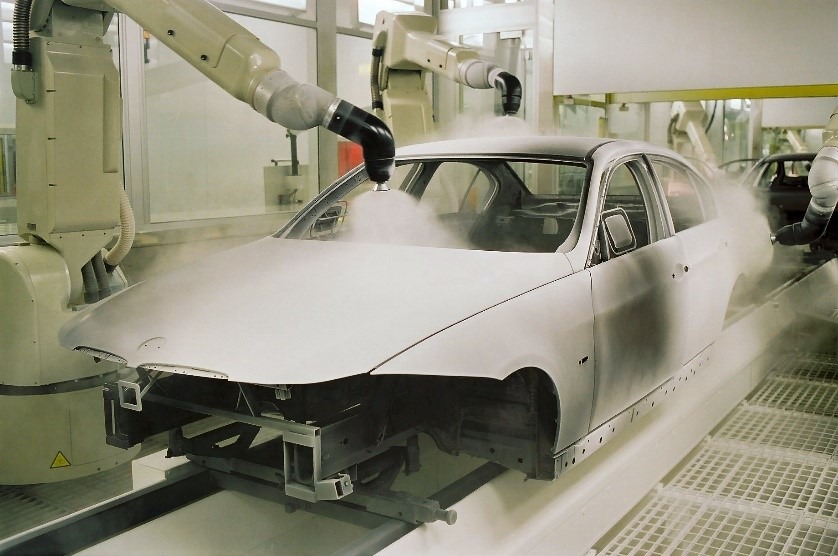
Deckbeschichtung
Erst jetzt bekommt die Karosserie mit dem so genannten Basislack (ca. 0.015 Millimeter) ihre Farbe. In den Automobilwerken lackieren Lackierroboter die komplette Karosserie in den jeweils aktuellen Farbtönen. Diese heute wasserbasierten Lacksysteme können Effektpigmente oder – wie im Falle einer Metallic-Lackierung – Aluminiumplättchen enthalten. Für die Lackierroboter schwer erreichbare Stellen werden von Lackierern direkt am Ende der Lackierstraße nachgearbeitet. Zwar hat der Wagen jetzt seine Farbe, doch der Glanz fehlt noch. Der Glanz entsteht durch das Aufspritzen eines farblosen Klarlacks ( ca. 0.040 Millimeter), welcher der Karosserie ihr glänzendes Aussehen verleiht und das Design des Fahrzeugs so richtig zur Geltung bringt. Der Klarlack hat aber auch die Funktion, die farbegebende Beschichtung vor äußeren Einflüssen, wie UV-Strahlung, organischen oder chemischen Verschmutzungen oder sonstigen Beschädigungen zu schützen. Ohne ihn würde sich der Farbton der Lackierung allein durch das Licht der Sonne allmählich verändern.
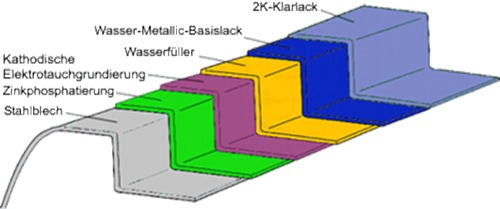
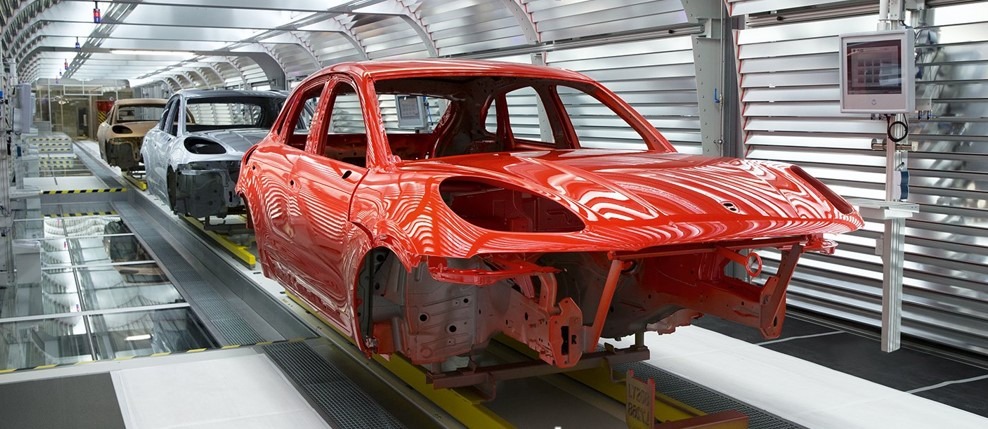